Our Products
Excellence in Quality and Innovation, Trusted Leader in Production of Various Rubber Products
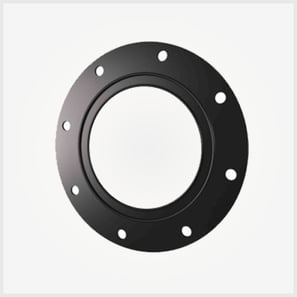
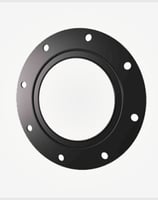
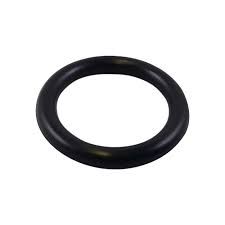
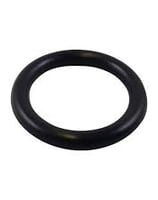
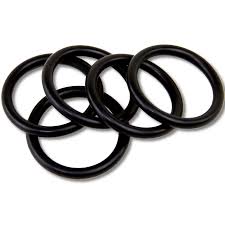
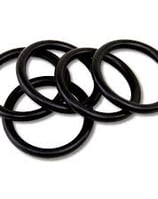
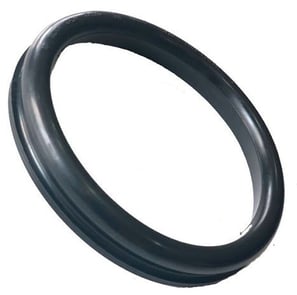
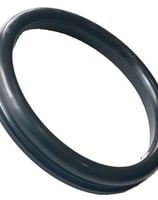
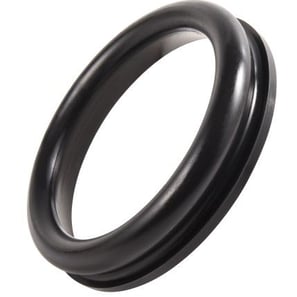
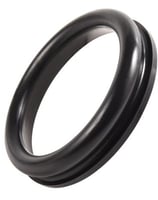
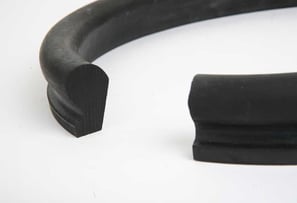
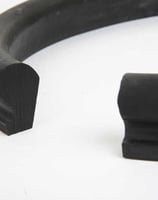
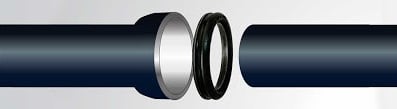
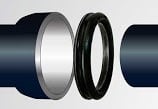
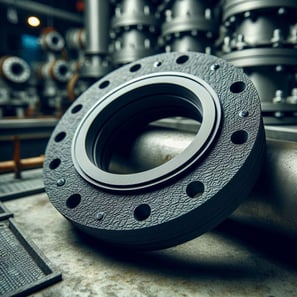
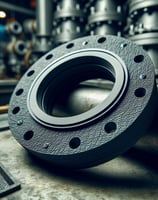
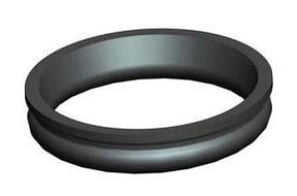
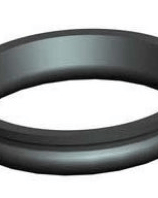
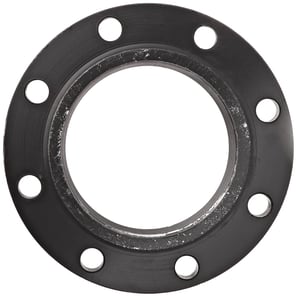
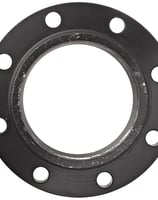
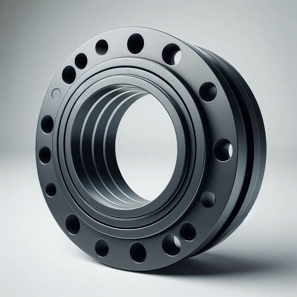
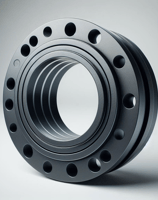
Product Details
Common types of rubber materials used include:
- Nitrile (NBR): Good resistance to oils and fuels.
- EPDM (Ethylene Propylene Diene Monomer): Excellent resistance to weather, ozone, and aging, as well as hot and cold water.
- Silicone: Good temperature resistance and flexibility.
- Viton (FKM): High chemical resistance and excellent performance at high temperatures.
Flange gasket rubber rings
These gaskets come in various sizes and thicknesses to fit different flange standards, such as ANSI, DIN, or JIS. Proper selection of the rubber material and dimensions is crucial to ensure a reliable and durable seal.
Types of Flange Gaskets:
1. Full-Face Gaskets: Cover the entire face of the flange, including the bolt holes.
2. Ring-Type Gaskets (RTJ): Fit inside the bolt circle, covering the area between the bolts.
3. Spiral Wound Gaskets: Made from alternating layers of metal and filler material, providing excellent sealing performance.
4. Corrugated Metal Gaskets: Made from corrugated metal, sometimes with a soft covering, used for high-pressure and high-temperature applications.
5. Sheet Gaskets: Cut from sheets of material like rubber, graphite, or PTFE.
Materials:
1. Rubber (Nitrile, EPDM, Neoprene, Silicone, Viton): Suitable for various chemical and temperature conditions.
2. Graphite: Good for high-temperature applications.
3. PTFE (Teflon): Excellent chemical resistance and suitable for high temperatures.
4. Metal (Stainless Steel, Copper, Monel): Used in applications requiring high strength and durability.
Pressure and Temperature Ratings:
• Pressure Ratings: Flange gaskets are rated to handle different pressure classes, typically ranging from Class 150 to Class 2500 (or equivalent in other standards).
• Temperature Ratings: Depending on the material, flange gaskets can handle a wide range of temperatures, from cryogenic temperatures up to several hundred degrees Celsius.
Size Range:
• Standard Sizes: Conform to various standards like ANSI, ASME, DIN, JIS, and others. Common sizes range from ½ inch to 24 inches and above.
• Custom Sizes: Can be manufactured to meet specific requirements beyond standard sizes.
Applications:
1. Oil and Gas Industry
2. Chemical Processing
3. Power Generation
4. Water Treatment
5. Food and Beverage Industry
Selecting the appropriate flange gasket requires considering the specific requirements of the application, including chemical compatibility, temperature, pressure, and flange.
Reinforced Cement Concrete
At J D Rubber manufacturing of RCC (Reinforced Cement Concrete) pipes for Horizontal and Vertically cast pipes, NP1, NP2, NP3, NP4 are commonly used in construction for drainage, sewage, and water supply systems. Rubber rings, or rubber gaskets, are crucial components used to ensure watertight and airtight seals between pipe joints.
Here’s a brief overview of RCC pipe rubber rings:
1. Material : These rubber rings are typically made from high-quality elastomers like natural rubber, EPDM (Ethylene Propylene Diene Monomer), or other synthetic rubbers that provide durability and flexibility.
2. Function : The primary function of these rings is to prevent leakage at the joints of RCC pipes by creating a tight seal. They accommodate minor movements and expansions due to temperature changes and ground movements.
3. Installation : During installation, the rubber rings are placed in the grooves or recesses at the ends of the pipes. When the pipes are pushed together, the rings compress to form a seal.
4. Standards : The rubber rings used in RCC pipes often comply with various standards and specifications to ensure quality and performance, such as IS 5382 (Indian Standard) or BS EN 681 (British Standard) suitable for pipes as per IS 458.
5. Benefits :
Leak prevention : Ensures no water or sewage escapes from the joints.
Flexibility : Can absorb minor shifts and movements.
Durability : Resistant to various environmental conditions and chemicals.
6. Size Range : 100mm to 2600mm diameter
Proper selection and maintenance of these rubber rings are essential for the longevity and functionality of RCC pipe systems.
PSC pipes
Prestressed Concrete Cylinder (PSC) pipes typically use rubber seals to ensure watertight joints. These seals are crucial for maintaining the integrity of the pipeline and preventing leaks. Here's an overview of how these rubber seals work:
Types of Rubber Seals
1. Gasket Seals: Commonly used in joints between pipe segments. They are usually made from durable rubber compounds like Natural Rubber (NR), EPDM (ethylene propylene diene monomer) or NBR (nitrile butadiene rubber), known for their flexibility and resistance to aging, weathering, and chemicals
2. O-Ring Seals: Often used in smaller diameter pipes or specific joint types where a tight seal is required. These are circular and fit into grooves on the pipe ends.
3. Profile Seals: These have a specific cross-sectional shape designed to fit into corresponding grooves on the pipe ends, providing a tight seal.
Installation Process
1. Cleaning: The pipe ends and grooves are thoroughly cleaned to ensure there is no debris that could compromise the seal.
2. Lubrication: A suitable lubricant is applied to the rubber seal to facilitate easy fitting and to prevent damage during installation.
3. Placement: The rubber seal is placed into the groove of one pipe end.
4. Joining: The pipes are then aligned and pushed together. The rubber seal compresses, creating a watertight seal.
Maintenance and Inspection
Regular inspection of PSC pipes and their seals is essential to ensure long-term performance. Maintenance may include:
- Visual Inspections: Checking for visible signs of wear, tear, or damage.
- Leak Detection: Monitoring for any signs of leakage at the joints.
- Seal Replacement: If a seal is found to be damaged, it should be replaced promptly to maintain pipeline integrity.
These seals play a critical role in the overall functionality of PSC pipes, ensuring they remain watertight and efficient throughout their service life.
Applications of PSC pipe Rubber Rings :
Rubber rings in Prestressed Concrete Cylinder (PSC) pipes are critical components for ensuring watertight joints in various applications. Here are some of the primary applications:
1. Water Supply Systems
- Municipal Water Distribution: PSC pipes with rubber rings are commonly used in municipal water supply systems to transport drinking water from treatment plants to residential and commercial areas.
- Long-Distance Water Transport: They are ideal for long-distance water conveyance due to their durability and ability to maintain high-pressure integrity.
2. Sewage and Wastewater Systems
- Sewage Treatment Plants: PSC pipes are used to convey sewage from residential and industrial areas to treatment plants.
- Stormwater Drainage: They are employed in stormwater management systems to handle large volumes of runoff, especially in urban areas.
3. Irrigation Systems
- Agricultural Irrigation: PSC pipes with rubber rings are used in large-scale irrigation projects to distribute water efficiently to agricultural fields.
- Canal Systems: They are often used in lining canals and distributing water through complex irrigation networks.
4. Industrial Applications
- Cooling Water Systems: Industries use PSC pipes to transport cooling water, especially in power plants and manufacturing facilities.
- Process Water Supply: They are employed in various industrial processes requiring a reliable water supply.
5. Firefighting Systems
- Hydrant Systems: PSC pipes with rubber seals are used in fire hydrant networks, ensuring a reliable water supply for firefighting purposes.
6. Hydroelectric Power Plants
- Penstocks: PSC pipes are used in penstocks to transport water from reservoirs to turbines in hydroelectric power plants, leveraging their strength and durability.
7. Infrastructure Projects
- Bridges and Tunnels: PSC pipes are used in infrastructure projects for drainage and water management systems within bridges and tunnels.
Benefits of Using PSC Pipe Rubber Rings in These Applications
- Leak Prevention: The rubber rings ensure watertight joints, preventing leakage and water loss.
- Flexibility: They accommodate minor movements and vibrations without compromising the seal, which is essential in dynamic environments.
- Ease of Maintenance: Rubber ring seals simplify the inspection and maintenance process, making it easier to identify and fix potential issues.
- Longevity: High-quality rubber rings contribute to the long service life of PSC pipe systems, ensuring reliable operation over extended periods.
The use of rubber rings in PSC pipes enhances the efficiency, reliability, and longevity of pipeline systems across various sectors, making them a preferred choice for critical water and wastewater infrastructure projects.
Benefits of PSC pipe Rubber Rings
Rubber rings in Prestressed Concrete Cylinder (PSC) pipes provide several benefits that enhance the functionality, reliability, and longevity of pipeline systems. Here are the key benefits:
1. Watertight Sealing
Leak Prevention: Rubber rings ensure a tight, watertight seal at the joints of PSC pipes, preventing leaks and reducing water loss.
Pressure Resistance: They can withstand high internal and external pressures, maintaining the integrity of the seal under various conditions.
2. Flexibility and Adaptability
Movement Accommodation: Rubber rings can absorb and accommodate minor movements, vibrations, and shifts in the pipeline, reducing the risk of joint failure.
Thermal Expansion: They allow for thermal expansion and contraction of the pipes, minimizing stress on the joints.
3. Durability
Weather Resistance: High-quality rubber compounds like EPDM or NBR are resistant to aging, UV radiation, and weathering, ensuring long-term performance.
Chemical Resistance: These rubber rings can withstand exposure to various chemicals, making them suitable for diverse environments, including wastewater and industrial applications.
4. Ease of Installation
Simplified Joining: Rubber rings simplify the process of joining PSC pipe segments, reducing the time and labor required for installation.
Less Equipment Needed: The installation process with rubber rings typically requires fewer tools and equipment, making it more efficient and cost-effective.
5. Maintenance and Inspection
Ease of Inspection: Rubber ring joints are easier to inspect for signs of wear or damage, facilitating regular maintenance routines.
Replacement Simplicity: If a seal is compromised, rubber rings can be replaced relatively easily compared to other sealing methods, minimizing downtime and repair costs.
6. Cost-Effectiveness
Reduced Leakage Costs: By preventing leaks, rubber rings help reduce water loss and the associated costs of water treatment and delivery.
Extended Service Life: The durability and reliability of rubber rings contribute to the extended service life of PSC pipe systems, reducing the need for frequent repairs or replacements.
7. Environmental Benefits
Reduced Water Waste: Effective sealing with rubber rings helps conserve water by minimizing leaks and ensuring efficient water delivery.
Lower Maintenance Impact: The ease of maintenance and long service life reduce the environmental impact associated with frequent repairs and replacements.
8. Versatility
Wide Range of Applications: Rubber rings are suitable for various applications, including water supply, sewage and wastewater systems, irrigation, industrial processes, and firefighting systems.
Compatibility: They are compatible with different types of PSC pipes and joint configurations, providing a versatile sealing solution.
By providing reliable, durable, and easy-to-install seals, rubber rings play a crucial role in ensuring the efficient operation and longevity of PSC pipe systems across various sectors.
Di pipe gasket
Ductile iron pipes commonly use rubber gaskets for sealing joints. These gaskets provide a flexible, watertight seal, which is crucial for maintaining the integrity and performance of the piping system. Here are some key points about ductile iron(DI) pipe rubber gaskets:
Material : The rubber used is typically made from EPDM (Ethylene Propylene Diene Monomer) or SBR (Styrene-Butadiene Rubber). These materials are chosen for their durability, flexibility, and resistance to various environmental conditions.
Types : Common types of gaskets used include Tyton® gaskets and push-on gaskets. Tyton® gaskets are specifically designed for ductile iron pipes and offer a reliable seal.
Installation : Gaskets are placed in the bell (the enlarged end) of one pipe, and the spigot (the plain end) of another pipe is inserted into the bell, compressing the gasket to create a tight seal.
Applications : DI pipes with rubber gaskets are widely used in water supply and sewage systems due to their strength, durability, and leak-proof performance.
Standards : These gaskets must meet specific industry standards, such as IS:5382, AS681, ISO 4633, EN 681.
Maintenance : Regular inspection and maintenance are important to ensure the gaskets remain in good condition and continue to provide a proper seal over time.
Size Range : DN80 to DN 1200
DI pipe Tyton Gasket Advantages :
Tyton gaskets used in ductile iron (DI) pipes offer several advantages, making them a preferred choice for many piping systems. Here are some key benefits:
Superior Sealing : Tyton gaskets provide an excellent watertight seal, reducing the risk of leaks and ensuring the integrity of the piping system.
Ease of Installation : The design of Tyton gaskets allows for straightforward installation, often without the need for special tools. This can save time and reduce labor costs.
Flexibility and Movement Accommodation : These gaskets allow for a certain degree of pipe movement, which can be beneficial in accommodating thermal expansion, contraction, and ground movement without compromising the seal.
Durability : Made from high-quality materials like EPDM or SBR, Tyton gaskets are resistant to aging, weathering, and a wide range of chemicals. This ensures a long service life, even in challenging environments.
Standardization : Tyton gaskets conform to industry standards, such as those set by the American Water Works Association (AWWA), ensuring compatibility and reliability across different piping systems.
Versatility : Suitable for a variety of applications, including potable water, sewage, and industrial pipelines, Tyton gaskets provide versatility in their use.
Maintenance-Free : Once installed, Tyton gaskets typically require minimal maintenance, contributing to lower overall operating costs for the piping system.
Pressure Handling : These gaskets can handle high-pressure applications effectively, making them suitable for both low and high-pressure systems.
Overall, Tyton gaskets offer a reliable, cost-effective, and durable solution for sealing ductile iron pipes in various applications.